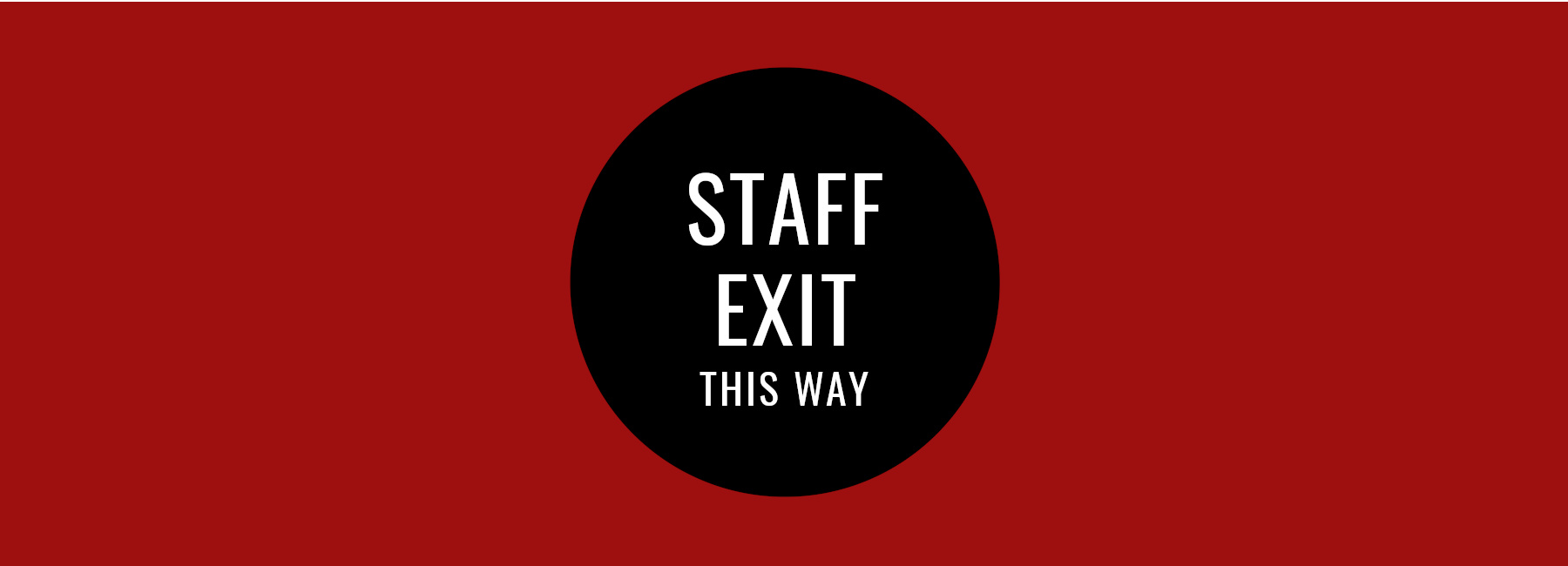
How important is workplace training to your business – and your employees?
Is your business doing enough to keep hold of its brightest talent? Is your business doing enough to progress its long serving employees in order to keep them motivated?
Keeping your workforce happy, productive and motivated is a constant challenge. You work hard to find and employ the right person, get them to accept your job offer and induct them into your organisation. Then the real work starts, keeping them engaged and delivering at an optimum level for the months and years to come. This can be difficult and failing to do so can have a negative impact on their willingness to remain in your employment (or you wanting to employ them!). It’s important to remember that happiness, motivation and productivity don’t just come because you are paying them to be there; even additional pay does not necessarily lead to employees feeling fulfilled and performing at the top of their game.
So the culture and environment you create for your employees is important. This may include a number of different factors such as conditions, support, workload, perks and incentives, all of which can help to ensure your employees are happy and less likely to look for another place to work. An employee’s ongoing personal and professional development can also be a factor, with opportunities to upskill being a big reason that employees stick around and offer you their best possible performance.
The phrase ‘fail to train, fail to retain’ is a reality with 56% of workers saying they would be prepared to leave an employer if high quality training isn’t offered. Employers with a low turnover of staff understand this and build a culture that gives opportunity to employees to train at every level. Businesses who fail to offer training increase their risk of employee churn, damaging their ability to grow, their ability to take advantage of opportunities and their ability to maintain quality in what they do or in what they produce.
Only 17% of engineering employers surveyed in the government’s Apprenticeship Evaluation 18/19 were using apprenticeships for existing employees. Now, that’s not to say that engineering employers are not offering training to their employees - it is fundamental and required for many aspects of work. However, for an industry with a high usage of apprenticeships to bring new talent into the sector, it is surprising that apprenticeships are not more widely used to develop those already employed. It is even more surprising when you consider how cost effective apprenticeships are both for those who pay the apprenticeship levy and those who do not.
Of course, whilst an apprenticeship can be cost effective, as with any training or CPD they carry other costs in terms of the employee’s time and productivity. That said, the cost of replacing someone (in terms of recruitment, induction, training them in your specific processes) can be far more than retaining a good staff member and offering them the opportunity of skill development. That feeling of progression will also spur an improvement in their personal performance, bring new ideas into the business and offer a general improvement in their ability to do their job.
Using apprenticeships to upskill and motivate your staff
Apprenticeships can offer opportunities at every level of a business, can be started at any age and at any time of the year. Here we look at an option for levels 2, 3 and 4:
Level 2 Lean Manufacturing Operative
This apprenticeship is for those working in a range of roles including production/assembly, inspection/quality, logistics/material handling or production processing/finishing. Level 2 is designed for those without a great deal of prior learning, it lasts 12 months and doesn’t have any college requirement as all the learning is done in the work place.
Level 3 Maintenance and Operations Engineering Technician
With several route ways through this apprenticeship including mechanical, electrical, electronic, instrumentation, controls/systems and plant/operations this apprenticeship has the flexibility to fit a variety of employees. It takes up to 36 months and the person gains a Level 3 Diploma in Advanced Manufacturing and Engineering through day release to college.
Level 4 Engineering Manufacturing Technician
Covering areas such as quality, production, procurement, costing, test/commissioning, installation, process and production support the apprenticeship takes up to 42 months and the person gains a Higher National Certificate in Engineering through day release at college. Completing an apprenticeship at this level is the equivalent of a foundation degree.
What is the best way to work out what apprenticeship might suit your employee?
Talk to us. That is the best way to pinpoint how you can use an apprenticeship for an existing member of staff. We will take time to understand what you want to achieve, what the employee is able to achieve and then match an apprenticeship to meet your criteria. We can walk you through the funding that is available, explain your responsibilities as an employer and outline how we will support you and the employee through every step.
Written by Mark, CEO.